|
|
Electric Aileron Trim
Servo
|
|
I've
decided to use a modified version of the optional electric aileron
trim. I will mount the electric servo as depicted in the
plans but I don't like the hinged trim tab hanging off the aileron
so I'll be designing and building a flush trim tab similar to the
elevator trim. I saw something similar on Dick Martins RV-8
and I'll attempt to re create it.
|
|
The trim
kit comes with a doubler plate to replace one of the A-408
plates. A bracket will be fabricated that will mount the
servo to this doubler plate. I drilled 4 holes in the
corners and used a Dremel tool with a cutoff wheel cut out the
square hole. I then used a pneumatic nibbler to try and
clean it up and that was a mistake. Wrong tool for the job
and the hole isn't nearly as clean as I'd like. It won't
be visible and it's solid so I'll use it.
|
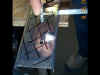
The
coping saw is a fast and easy way to cut square holes.
|
I also had to cut the
same size hole in the aileron spar. My friend Paul
suggested I use a copping saw for a more precise cut.
Considering how slopping the first one was, I gave it a try.
Worked like a champ. Just drill 4 holes in the corners and saw
away. I could have cut closer to the lines and saved
myself a bunch of filing but it turned out very nice
|
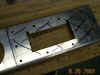
This
picture was taken after the doubler plate was mounted then
removed |
|
A mounting bracket
for the trim servo needs to be fabricated but I forgot to take a
picture of the fabrication process. Here is the end result
mounted to the aileron spar with nut plates.
|
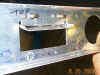 |
Trim
servo mounted in position for fit.
|
The servo
is matched drilled to the mounting bracket and installed on the
aileron spar. In these pictures the mounting bracket has
not been riveted yet. Everything still needs to be
primered.
The trim tab itself will be fabricated after the skin has
been drilled to the skeleton. I'll have that process
documented in the next couple of weeks |
|
After the
skin is riveted and dimpled, it's time to make the access
panel to access the servo. This is fabricated on the
leading edge of the aileron. I made a mistake that you can see
in this photo. I should not have drilled the rib since I
will be making a new cover plate. These holes in the rib
will cause me problems a little later.
|
|
The first step is
making a doubler plate for the access panel. Since the leading
edge has a nice curve in it I have to curve the double plate to
match. I couldn't figure out how to make the curve until I
saw a large piece of PVC sitting in the corner. With
thoughts of rolling cookie dough and how it sticks to the
rolling pin, I made a really cool curved plate. I then cut
it to size.
|
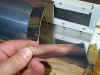 |
|
You can see in the
left picture how the curves didn't quite match so more rolling
took place. Let me warn you, make sure the rolled curve
matches aileron curve before riveting.......
|
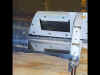 |
|
In this
picture it looks like everything is matched and ready for
riveting. There was a little difference in the curves
though and because the double plate is thicker than the
.016" aileron skin guess which one won when they were
riveted together.
|
The nutplate installation was a little messy
give the small area to work in
|
It's tough to see in
the left picture but there is a little flat spot. It won't
be noticeable to the air when flying but someone at a fly-in
somewhere will probably see it. Remember those extra holes
I drilled earlier? They got in the way when installing the
nut plates. I removed one of the flanges and replaced it
with a home made piece. Works great.
|
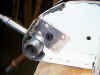
The
little rubber grommet is for the wires from the servo that will
exit. The wires will then run to the wing rib conduit. |
|
With the
cover all rolled, drilled and dimpled everything fits pretty
nice and looks good.
Now on to the hard part. Deviating from the plans to
make the trim tab itself. |
Aileron Trim
Construction
|
|
Instead of a hinged tab hanging off
the trailing edge of the aileron I decided to build and integral
tab ala the elevator trim. The first step is to cut out
the material where the trim tab will go. I drilled holes
in the corner prior to cutting but then decided I wanted the
trim tab a little larger hence the second set of holes. |
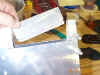
The
Dremel tool does a nice job of cutting the aileron skin. |
|
Next I had to make a "riblet"
to support the skin next to the stiffeners. The outboard
rib will the support the skin on the left side of the trim
tab. I used some modeling clay and plastic wrap to make a
mold for the shape of the "riblet". I removed the clay
and traced the outline on some cardboard to check for fit.
I then traced the outline on some aluminum then bent the
aluminum to size. |
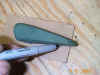 |
|
The finished "riblet" (sorry
for the picture quality) is shown and then the "riblet"
is installed and cleco'd in place. |
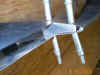 |
|
I forgot to take a picture, but I then
made a small trim spar out of some extra .016" sheet that
can be seen in the picture on the left. I also cut and
installed the trim tab hinge and hinge pin locking device at
this point. |
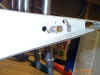
Nut plate and hinge
eyelet work well to secure the trim tab hinge pin. |
Construction of Trim Tab
|
|
The first
step to making the trim tab was to layout the shape. I
determined the shape by making a mock up on a piece of flexible
cardboard. After a couple of tries, I came up with a
design and size that I thought would work. As it turned
out, it took me 3 tries on different pieces of aluminum sheet to
get the trim tab shape and size correct. |
|
These pictures show
the little trim tab spar (a U shaped piece of .016"
aluminum) and half of the hinge piece being positioned for fit. |
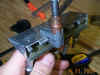 |
|
This is
the completed trim tab. This is my second try at
installing a control horn for the clevis to attach. I used
a large piece of hinge and cut down one of the eyelet to
1/4". The hinge pin diameter for this particular
hinge is 1/8", the same size as the clevis pin. It
works perfect. |
|
The aileron side of
the trim tab can be seen here, both before and after the spar
installation. I used a Unibit to cut a hole in the spar
for the trim control rod, then filed the opening to size. |
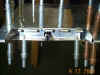 |
|
Here is
the trim tab installed and hooked up. Now I can
disassemble the aileron, debur, dimple then rivet everything
together. |
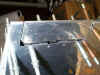
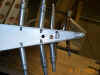
The
trailing edge shows that the tab is nice and even with the
aileron. Lots of work.
|
|
These three pictures
show the completed and riveted trim tab installation. The
movement is very smooth (not bad it only took 4 tries).
I've done all my testing with an older style MAC 8 Servo which
has a travel length of 1.2". I'll be installing a
different servo that has a travel limitation of .5" which
will provide plenty of trim tab travel but won't try to bend the
thing to pieces or cause any
serious problems in a "runaway tab" scenario. |
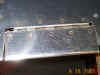 |