|
|
|
Main Rib Preparation |
 |
Wing rib preparation starts
right here....In my case the dining room table. I spent about 6 hours over
the course of 2 days marking, straightening and fluting ribs and I still
had to debur them. This is boring and tedious work so I brought
them all upstairs to the kitchen table so I could spend some quality time
with my wife (Beth) and still work on the plane.
It would have only taken one scratch on the kitchen
table to wipe the slate clean on that nice gesture. I got lucky, not
a mark. |
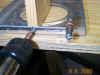 |
The process of drilling the main ribs starts
with locating the center of each rib flange. To do this, I use a
centering ruler to mark the center point. It works great! The next step is to make a template out of a piece of stiffener
angle. Follow the plans for spacing and you should not have a
problem with any of the holes going through the main spar flange strips.
Use the template to drill all the main ribs on the end that attaches to the main spar.
You'll drill the aft end of the main ribs using another template later.
I then clamped the template to the rib flange and lined the center of the rib up with a mark
on the template. I used a piece of wood to back up the rib flange
while I drilled the holes. I was able to drill all the main ribs (28) in about a half hour.
|
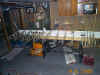
|
The Orndorff videos and other
builder web sites, show the wing
skeleton being assembled on the wing jigs. Vans recommends in the
construction manual and via phone call, that it's probably easier to
assemble, drill and cleco the wings on a work surface then use the jigs to
true up the skeleton and final assembly. It makes sense to me and
that's how I'm doing it.
|
Aileron
Bell Crank & Rib Assembly
|
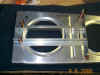 |
After cutting the bell crank attachment angles
I measured and used a 2x4 (1.5" x 3.5") to set the spacing
of the angles then drilled and cleco'd them in place.
For only the second time since starting the kit, I used the vixen file
to file away the ends of the attachment angle so they would fit flush on
rib when overlapping the rear angle.
Here is the completed bell crank attachment angles drilled and cleco'd
to the rib. |
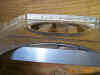 |
The manual doesn't discuss what to do with the
rivets that you can't get to. I'll probably just drill a hole in the
rib that is large enough to get the squeezer through. The other
option is to counter sink the angle and rivet the pieces before attaching
the assembly to the rib. |
|
The bell crank pieces are steel and didn't come
powder coated so I primed them early in the process when I primed the main
spars.
Here, I clamped the pieces together with the bearing and drilled the
bearing mounting holes. Don't forget to mark the bearing and the bell crank
so you can line the holes up after disassembly.
Initially I couldn't figure out how do drill a perpendicular hole for
the heim ends. I stuck a 1/2" piece of plywood in between the
metal pieces and drilled them all as one assembly. This ensured that
both holes were the same because the metal didn't flex when
drilling. It's little victories like this that make the project fun.
The bearing leaves a gap in the metal brackets so the plans call for a
.063 x 1/2 x 1.5 piece of aluminum to be riveted in place. Actually,
the plans are rather vague here. They didn't supply the pieces in
the parts bag so I cut up a .063x3/4x3/4 piece of angle to make the pieces
The finished aluminum strips drilled and cleco'd in place. |
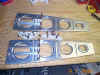 |
The completed bell cranks and ribs. All parts still
need to be primed before riveting. |